Introduction
Copper extraction from its ore is a complex process involving multiple stages, from mining and crushing to concentration and refining. This flow chart provides a detailed breakdown of the copper extraction process, highlighting key steps and the equipment required—including Liming Heavy Industry’s high-efficiency crushing solutions.
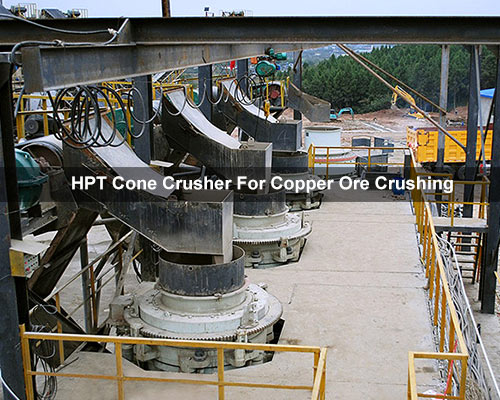
Step-by-Step Copper Extraction Flow Chart
1. Mining Copper Ore
Copper ores like chalcopyrite (CuFeS₂), bornite (Cu₅FeS₄), and chalcocite (Cu₂S) are extracted via open-pit or underground mining techniques.
2. Primary Crushing
The ore is transported to a primary crusher, such as the Liming C6X Jaw Crusher (a high-capacity model for coarse crushing). This reduces large ore rocks into smaller pieces (typically 6–8 inches in diameter).
3. Secondary & Tertiary Crushing
For finer crushing, copper ore passes through:
- Secondary crusher: Liming HPT Cone Crusher (ideal for medium-hard materials).
- Tertiary crusher: Liming VSI6X Sand Maker or HST Cone Crusher for further size reduction (<25mm).
4. Grinding (Ball Mill/Powdering)
Crushed ore is ground into fine powder using a ball mill or Liming MTW European Trapezium Grinding Mill to liberate copper minerals from waste rock.
5. Froth Flotation (Concentration)
The powdered ore undergoes froth flotation, where chemicals separate copper-rich froth from gangue.
6. Smelting & Refining
- Smelting: Concentrates are melted in a furnace (producing ~99% pure matte copper).
- Electrolysis: Final purification via electrowinning yields 99.99% pure copper cathodes.
7. Waste Management
Tailings are processed to minimize environmental impact.
Why Choose Liming Heavy Industry’s Crushing Equipment for Copper Mining?
Our jaw crushers (C6X Series), cone crushers (HPT/HST Series), and grinding mills (MTW Series) are:
- Highly efficient in ore size reduction.
- Energy-saving with durable designs.
- Globally trusted in mining operations.